Servo Motor
Testing Systems for Servo Motors
A Servo Motor is a closed-loop servomechanism that uses position feedback (like encoder) to control its motion and final position. The input to its control is a signal (either analog or digital) representing the position commanded for the output shaft. Servo Motors are used in radio-controlled airplanes to position control surfaces like elevators, rudders, walking a robot, or operating grippers.
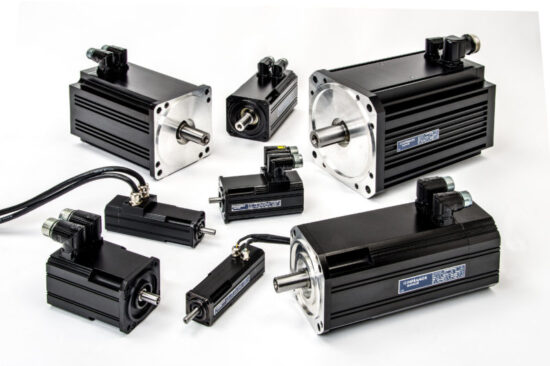
Servo Motor
Advantages
- Excel at position and speed control.
- High output power relative to motor size and weight.
- Encoder determines accuracy and resolution.
- High efficiency. It can approach 90% at light loads.
- High torque to inertia ratio. Servo Motors can rapidly accelerate loads.
- Achieve high speeds at high torque values.
- Quiet at high speeds.
Disadvantages
- Requires tuning to stabilize the feedback loop.
- Will become unpredictable when something breaks, so safety circuits are required.
- Complex controller requires encoder and electronic support.
- Peak torque is limited to a 1% duty cycle. Servo Motors can be damaged by sustained overload.
- Gear boxes are often required to deliver power at higher speeds.
- Higher overall system cost and the installation cost of a Servo Motor system may be higher than that of a stepper motor due to the requirement for feedback components.
Maximizing Precision
Leveraging Motomea for Servo Motor Testing
The Motomea Regenerative Dynamometer System (Motomea RDS) enables:
- Complete load performance testing:
- Torque, Speed, Current, Efficiency, Power Input, Power Output.
- Standard electrical parameters testing:
- HV, Vibration, Noise, and others.
- Additional testing:
- Cogging, Back EMF, Friction, Friction Spectrum, Torque Ripple.
- Automatic temperature rise test:
- Thermocouple and/or PT100 device with 2 to 16 channels for Current, Voltage, Speed, Torque, Power Input, Power Output, all synchronized to each temperature reading.
- Electric Motorcycle/Scooter Motor Drive Cycle Load Simulation:
- Real-time simulation with acceleration, braking, change of vehicle states.
- Battery Simulation:
- Battery cycle testing (Charge/Discharge).
- Battery SOC (State Of Charge) script.
- Battery SOD (State Of Discharge) script.
- Special feature: Low voltage dip at current transient.
- System includes Output Filter with high capacitance
- Testing at U mode: Voltage Control (CV).
- Battery Testing:
- I+ mode: Current Control (CC+).
- I- mode: Current Control (CC-).
- P mode: Power Control (CP), CC-CV, Step for cut-off condition (ET, EV, EC, CC time, CV time, Cap%, etc.).
- Protection (OV & LV, OC & LC, OT).
- Additional EM Tests:
- Performance Generating Mode & Performance Motoring Mode.
- Stall Torque, Cogging Torque.
- Back EMF RMS, Open Circuit Back EMF, Back EMF Constant KE.
- No Load Coupled & Uncoupled.
- Torque Ripple Measurements at Low RPM & at High RPM.
- Electromechanical Time Constant.
- Voltage and Current Harmonics.
- Load from Excel File.
- Speed Torque Scope Viewer.
- Deceleration Test (MOI Calculation).
- Servo Bandwidth (Speed Loop & Current Loop).
- Dynamic Testing during acceleration and deceleration.
- Friction vs. Speed, Friction Drag Torque.
- Torque Speed FFT.
- Performance at Variable Voltage.
- Inductance Test 3 Phases.
- Vibration.
- ISG Tests: Generation Characteristic.
- ISO Efficiency Tests: ISO Efficiency and ISO Efficiency Contour.
- S1 to S8 – IEC duty cycles of operation for electrical motors.
Servo Motor
Advantages
- Excel at position and speed control.
- High output power relative to motor size and weight.
- Encoder determines accuracy and resolution.
- High efficiency. It can approach 90% at light loads.
- High torque to inertia ratio. Servo Motors can rapidly accelerate loads.
- Achieve high speeds at high torque values.
- Quiet at high speeds.
Disadvantages
- Requires tuning to stabilize the feedback loop.
- Will become unpredictable when something breaks, so safety circuits are required.
- Complex controller requires encoder and electronic support.
- Peak torque is limited to a 1% duty cycle. Servo Motors can be damaged by sustained overload.
- Gear boxes are often required to deliver power at higher speeds.
- Higher overall system cost and the installation cost of a Servo Motor system may be higher than that of a stepper motor due to the requirement for feedback components.
Maximizing Precision
Leveraging Motomea for Servo Motor Testing
The Motomea Regenerative Dynamometer System (Motomea RDS) enables:
- Complete load performance testing:
- Torque, Speed, Current, Efficiency, Power Input, Power Output.
- Standard electrical parameters testing:
- HV, Vibration, Noise, and others.
- Additional testing:
- Cogging, Back EMF, Friction, Friction Spectrum, Torque Ripple.
- Automatic temperature rise test:
- Thermocouple and/or PT100 device with 2 to 16 channels for Current, Voltage, Speed, Torque, Power Input, Power Output, all synchronized to each temperature reading.
- Electric Motorcycle/Scooter Motor Drive Cycle Load Simulation:
- Real-time simulation with acceleration, braking, change of vehicle states.
- Battery Simulation:
- Battery cycle testing (Charge/Discharge).
- Battery SOC (State Of Charge) script.
- Battery SOD (State Of Discharge) script.
- Special feature: Low voltage dip at current transient.
- System includes Output Filter with high capacitance
- Testing at U mode: Voltage Control (CV).
- Battery Testing:
- I+ mode: Current Control (CC+).
- I- mode: Current Control (CC-).
- P mode: Power Control (CP), CC-CV, Step for cut-off condition (ET, EV, EC, CC time, CV time, Cap%, etc.).
- Protection (OV & LV, OC & LC, OT).
- Additional EM Tests:
- Performance Generating Mode & Performance Motoring Mode.
- Stall Torque, Cogging Torque.
- Back EMF RMS, Open Circuit Back EMF, Back EMF Constant KE.
- No Load Coupled & Uncoupled.
- Torque Ripple Measurements at Low RPM & at High RPM.
- Electromechanical Time Constant.
- Voltage and Current Harmonics.
- Load from Excel File.
- Speed Torque Scope Viewer.
- Deceleration Test (MOI Calculation).
- Servo Bandwidth (Speed Loop & Current Loop).
- Dynamic Testing during acceleration and deceleration.
- Friction vs. Speed, Friction Drag Torque.
- Torque Speed FFT.
- Performance at Variable Voltage.
- Inductance Test 3 Phases.
- Vibration.
- ISG Tests: Generation Characteristic.
- ISO Efficiency Tests: ISO Efficiency and ISO Efficiency Contour.
- S1 to S8 – IEC duty cycles of operation for electrical motors.
See how we test a Servo Motor
WHY IS IT CRITICAL TO TEST Servo MotorS?
- Performance Assurance: Ensures servo motors meet speed, torque, and accuracy specifications.
- Quality Control: Identifies manufacturing defects or deviations early in production.
- Safety: Reduces risks of accidents or equipment damage.
- Optimization: Provides data for design efficiency and longevity.
- Customer Satisfaction: Builds trust and enhances reputation.
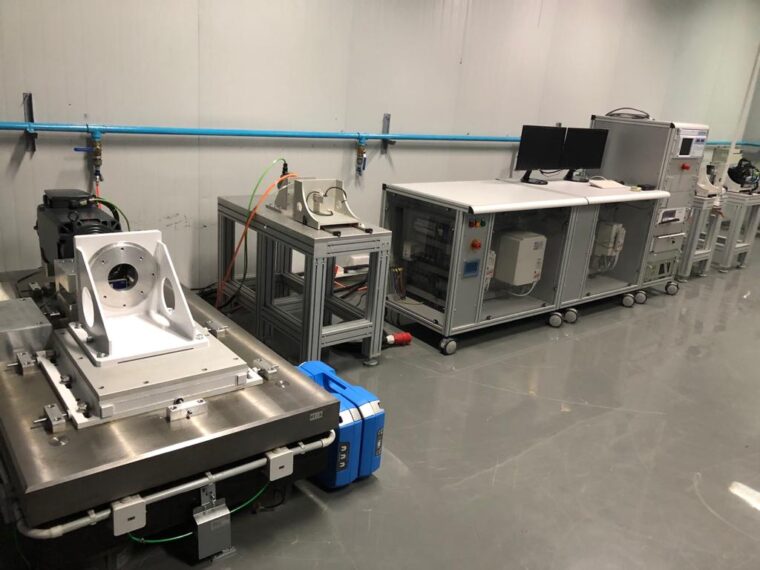
MOTOMEA invites you to contact us!
Ready to elevate your motor testing and predictive maintenance strategies? We're here to help. Whether you have questions about our solutions, need personalized advice, or want to explore partnership opportunities, we're just a message away. Connect with us today to unlock the full potential of your operations and drive success in the world of motor testing and predictive maintenance. Let's innovate together!